Three-phase AC motors as ideal drives for RACO electric Actuators
Our asynchronous three-phase AC motors, with a low moment of inertia, are ideal for accelerating large masses and intermittent operation (S3). Their modular design enables a wide range of variants, from 2 to 8 poles and in special voltages.
Special options include our robust RACO Electronic Position Sensor (EPS) and the innovative RACOmatic®.
- As a standard, they both offer IP54 protection, ISO F insulation class, and a thermal contact for thermal overload protection
- As an option, we can offer IP65 protection, ISO H insulation class, and a PTC thermistor
Our brake motors have controls installed in the terminal box for fast response behavior and short application times, which ensures low overrun and self-locking.
Precise Positioning with RACO Sensors
Our RACO sensors offer the ideal solution for controlling, regulating, and monitoring electric actuators, linear drives, and rotary drives. From electronic sensors to certified absolute encoders with fieldbus interface, we cover a wide range of requirements. The encoder systems used by RACO fulfill the standards in the automotive industry, as well as in mechanical and plant engineering.
RACO electronic Displacement Sensors EPS:
- Precise positioning of electromechanical linear drives
- Non-contact position detection via magnetic field coupling
- Safe operation even in the event of a power failure thanks to an on-board lithium battery
- Provides features of a multi-turn absolute encoder with digital signals and output of the set-point as an analog signal
Mechanical Limit Switches, Rotary Angle Transducers, Potentiometers:
- Alternative solutions for specific applications
- Ideal for explosion-proof environments
- Can be combined with rotary encoders or potentiometers
Certified Absolute Encoders with Fieldbus:
- Adapter for other encoder systems with fieldbus interface or safety encoders with SIL certification
- Increased safety for systems and personnel
- Certified according to current standards (IEC 61508 / EN 62061, EN ISO 13849-1)
- Guarantee of high reliability of the safety products
The actual valid Machinery Directive requires the distributor to carry out a detailed assessment of the safety of the system or process. Influences on the operating process, the operator, and the environment are defined as a hazard level for the safety requirements, which must then be technically fulfilled.
Electronic Position Sensor EPS 02
The basic version EPS02 enables the monitoring of end positions by means of 2 adjustable relay contacts in teach-in mode. The end positions are not traversable and therefore provide a high degree of operational safety. Compared to a classic design with mechanical limit switches and an individually adaptable manual transmission, the installation, commissioning, maintenance and upgrade are simplified.
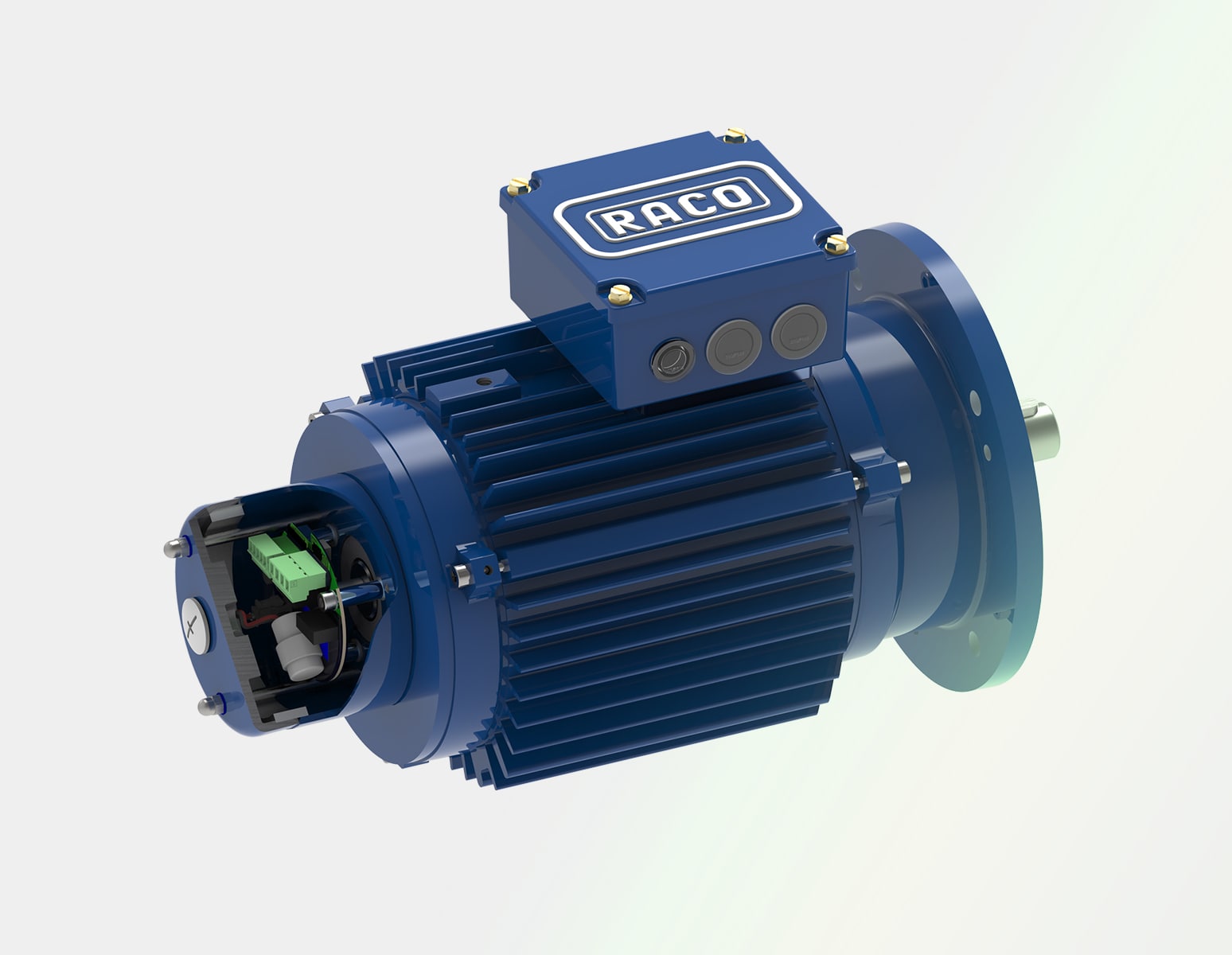
- Non-contact, wear-free sensor system
- Digital resolution < 0.01 mm
- Battery buffering in the case of a power failure (service life >10 years)
- Integrated evaluation of thermal contact / PTC thermistor sensor
- Switching points adjustable in the teach-in
Electronic position sensor EPS 06 with analogue position feedback
With the RACO displacement sensor EPS 06, additional functions have been integrated into the proven RACO position sensor. An additional interface board has created space for further analogue and digital outputs and additional functionality.
In addition to the 2 end position monitors (relay contacts), there are 4 adjustable intermediate positions, a calibratable analogue position feedback, position feedback and an electronic overload cut-off (UPM function) with adjustable time for start-up override and speed cut-off. Effective in both directions and locking in the overload direction.
Parameterisation is carried out via an intuitive Windows PC program with a connection via a USB cable supplied. The software is used to diagnose and parameterise the switching points and their function.
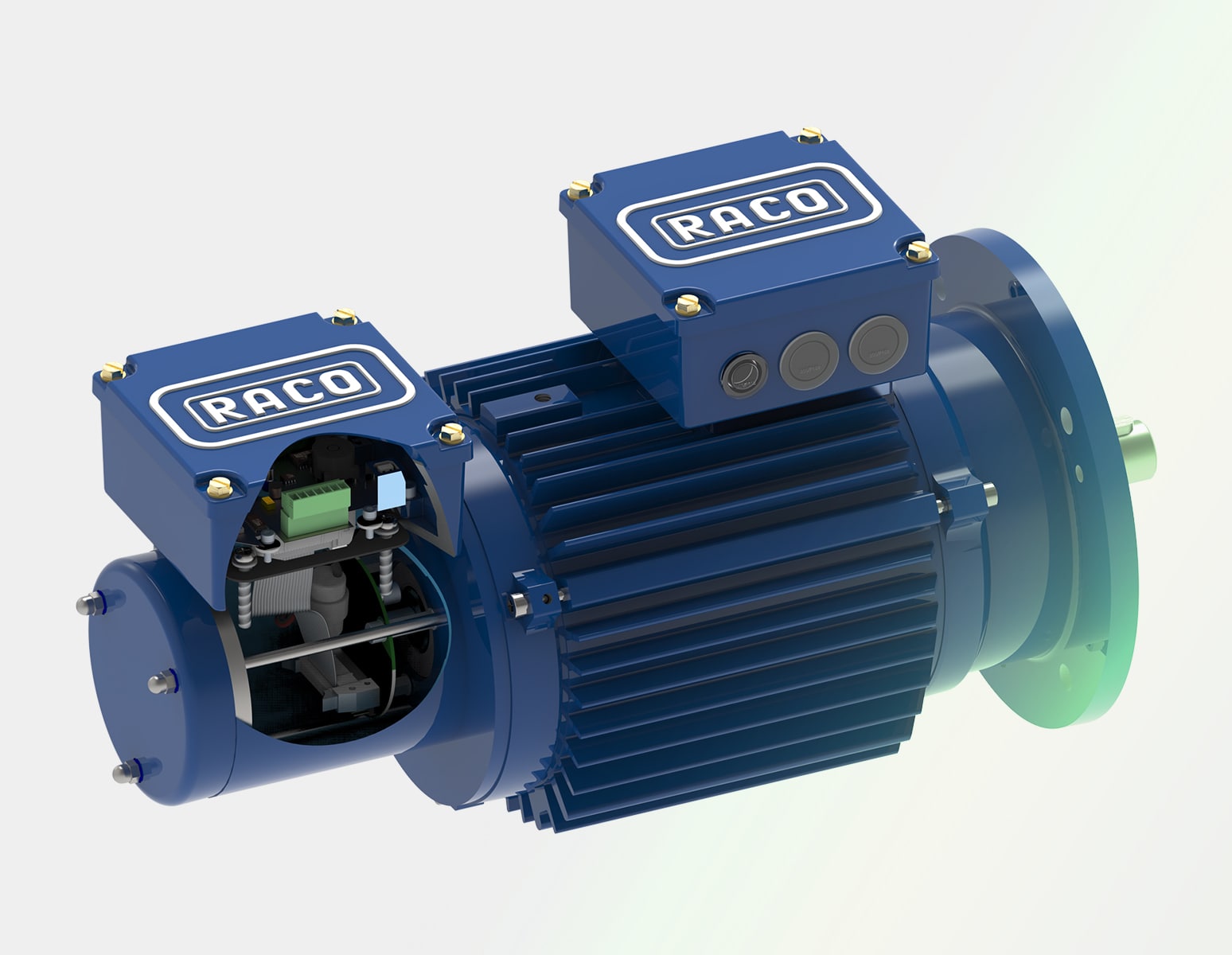
- Technical highlights of the EPS 06 displacement sensor
- Non-contact, wear-free sensor system
- Digital resolution < 0.01 mmBattery backup in the event of power failure (service life > 10 years)
- Integrated evaluation of thermal contact / PTC thermistor sensor
- Parameterisation via PC-Windows software via galvanically isolated USB interface
- 2 end positions (relay outputs)
- 4 intermediate positions (npn transistor outputs 24 VDC)
- Analogue position feedback 0-10V or 0(4) ... 20 mA or PWM output
- Incremental encoder simulation track A,B up to 256 pulses per revolution
- UPM function - overload switch-off with adjustable limit values for the speed